Metal fabrication plays a vital role in industries such as construction, automotive, aerospace, and many more. It involves processes such as cutting, welding, bending, and assembling materials to create finished products. Among these processes, sheet metal bending is one of the most crucial steps, requiring precision, expertise, and the right equipment.
However, despite the importance of bending, metal fabrication comes with its own set of challenges. Inaccurate bends, material handling difficulties, tool wear, and poor edge finishes are just some of the common issues that manufacturers face. Overcoming these challenges is crucial to ensure efficient production, reduce material waste, and improve product quality.
This blog will explore some of the most common challenges in metal fabrication and how you can overcome them using high-quality sheet metal bending machine manufacturing and supplier products. Specifically, we will look at how advanced technology and machinery can solve problems related to bending precision, tool longevity, operational costs, and more. By the end of this post, you’ll understand how investing in the right equipment, such as those provided by Energy Mission, can lead to better outcomes for your business.
Understanding the Metal Fabrication Process
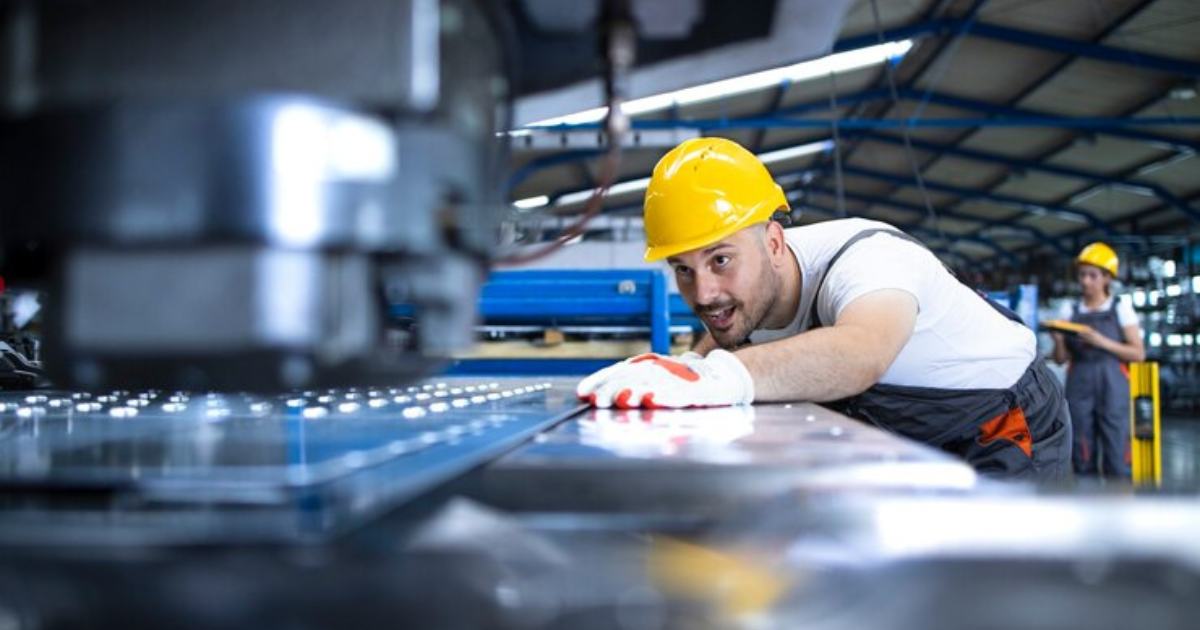
Before diving into the challenges of metal fabrication, it’s important to understand the basics of the process. Metal fabrication is a broad term that encompasses several techniques to shape raw metal into useful products. These processes include cutting, bending, welding, assembling, and finishing. Each step plays an essential role in the production of high-quality components.
Sheet Metal Bending is a key part of this process, particularly when working with materials like steel, aluminum, and copper. In sheet metal bending, a machine applies force to a sheet of metal to change its shape along a straight axis. This is done without removing any material but by deforming the sheet in such a way that it assumes a permanent bent shape. Precision is crucial here—whether you are creating a simple angle or a complex, multi-radius bend.
With the right equipment, like a sheet metal bending machine, manufacturers can achieve accurate, consistent, and repeatable results, making it easier to meet stringent design and quality standards.
Common Challenges in Metal Fabrication
Despite its widespread use, metal fabrication can be a complex and challenging process. Here, we highlight some of the most common issues that fabricators face and how the right equipment can help address them.
1. Inaccurate Bending Results
Problem: One of the biggest challenges in metal fabrication is achieving precise bending results. Inaccurate bends not only affect the appearance of the finished product but also impact the functionality, as it could lead to improper fitting parts, which then require costly rework.
There are several reasons for inaccuracies in bending, including:
- Material thickness variations
- Machine calibration issues
- Tooling problems
Solution: Choosing a high-quality sheet metal bending machine is crucial to ensuring accurate bending results. Advanced bending machines, like those provided by Energy Mission, are designed to provide consistent accuracy even with varying material thicknesses. These machines are equipped with advanced CNC controls that ensure the correct angle and force are applied, which minimizes the risk of errors. Additionally, regular calibration and maintenance of the bending machine are essential for long-term accuracy.
2. Tool Wear and Tear
Problem: Metal bending machines rely heavily on tools like dies and punches to create bends. Over time, these tools can wear down, leading to decreased performance and higher operational costs due to increased downtime for maintenance and tool replacements.
Solution: To overcome tool wear issues, it is essential to invest in high-quality tools and machinery. Energy Mission’s sheet metal bending machines are designed with durable, high-performance tools that are built to last. These machines help reduce wear and tear, leading to lower maintenance costs and fewer replacements. Additionally, choosing machines with automated tool changers and advanced settings for different bending operations can further improve machine longevity.
3. Material Handling Challenges
Problem: Handling large or heavy sheets of metal can be a significant challenge. Improper loading and unloading can lead to damage, inefficient handling, and increased labor costs. Moreover, metal sheets need to be precisely positioned to avoid any misalignment during the bending process.
Solution: One of the ways to tackle material handling challenges is by incorporating automated systems that streamline loading and unloading. Energy Mission offers machines that come with integrated material handling systems. These automated systems reduce the need for manual intervention, improving both safety and efficiency. Additionally, they help minimize the risk of damage during the bending process by ensuring proper material alignment.
4. Poor Edge Quality and Finish
Problem: Bending metal sheets often results in rough edges, burrs, or deformation, all of which negatively impact the quality and appearance of the final product. Such imperfections may require additional post-processing, increasing production time and costs.
Solution: A high-quality sheet metal bending machine can address these issues by providing better control over the bending process. Machines with high-precision features help create smooth, clean bends with minimal edge damage. Energy Mission’s machines, for example, come equipped with advanced edge control technology, ensuring that each bend is smooth and free from imperfections.
5. Limited Flexibility and Versatility
Problem: Traditional metal bending machines are often limited to handling specific materials or thicknesses, reducing their versatility. This can be a significant disadvantage for manufacturers who need to work with a variety of materials or complex designs.
Solution: To overcome this challenge, manufacturers should invest in versatile machines that can accommodate a wide range of materials, thicknesses, and bending configurations. Energy Mission offers sheet metal bending machines that are adaptable to different production requirements, providing flexibility for companies that need to bend a variety of materials or create custom designs.
6. High Operational Costs
Problem: Running metal fabrication operations can be expensive, especially when machines consume a lot of energy, require frequent repairs, or experience prolonged downtime. High operational costs can erode profit margins, making it harder for businesses to remain competitive.
Solution: Energy-efficient equipment is key to reducing operational costs. Modern sheet metal bending machine manufacturing and supplier products, like those from Energy Mission, are designed to reduce energy consumption while maintaining high performance. These machines are built with energy-saving features and low-maintenance components that help keep costs down in the long run.
How to Choose the Right Sheet Metal Bending Machine
Selecting the right sheet metal bending machine can be a daunting task, especially when considering the many factors that influence performance, cost, and long-term durability. When choosing a machine, keep the following factors in mind:
- Material Type and Thickness: Make sure the machine you choose can handle the materials and thicknesses you work with most often.
- Precision and Accuracy: Look for machines with advanced controls and features that ensure high levels of precision, especially for complex or intricate bends.
- Flexibility: Consider how versatile the machine is. Can it handle different types of bends, materials, and thicknesses without compromising on quality?
- Energy Efficiency: Opt for machines that are designed to save energy while providing maximum output.
- Budget and ROI: Although high-end machines can be more expensive, they often pay off in terms of long-term savings on maintenance, tool replacements, and energy costs.
Energy Mission’s sheet metal bending machine manufacturing and supplier services provide machines that meet these criteria, offering reliable, cost-effective solutions for businesses of all sizes.
Energy Mission Products: Providing Innovative Solutions
As a leader in the sheet metal bending machine manufacturing and supplier industry, Energy Mission is committed to providing high-quality machines that address the most pressing challenges in metal fabrication. Their products are engineered with precision, durability, and energy efficiency in mind, making them ideal for companies looking to enhance their metalworking operations.
From automated material handling systems to advanced edge control technology, Energy Mission offers solutions that reduce downtime, improve accuracy, and lower operational costs. By choosing Energy Mission, manufacturers can ensure that their metal fabrication process runs smoothly, efficiently, and profitably.
Best Practices for Effective Metal Fabrication
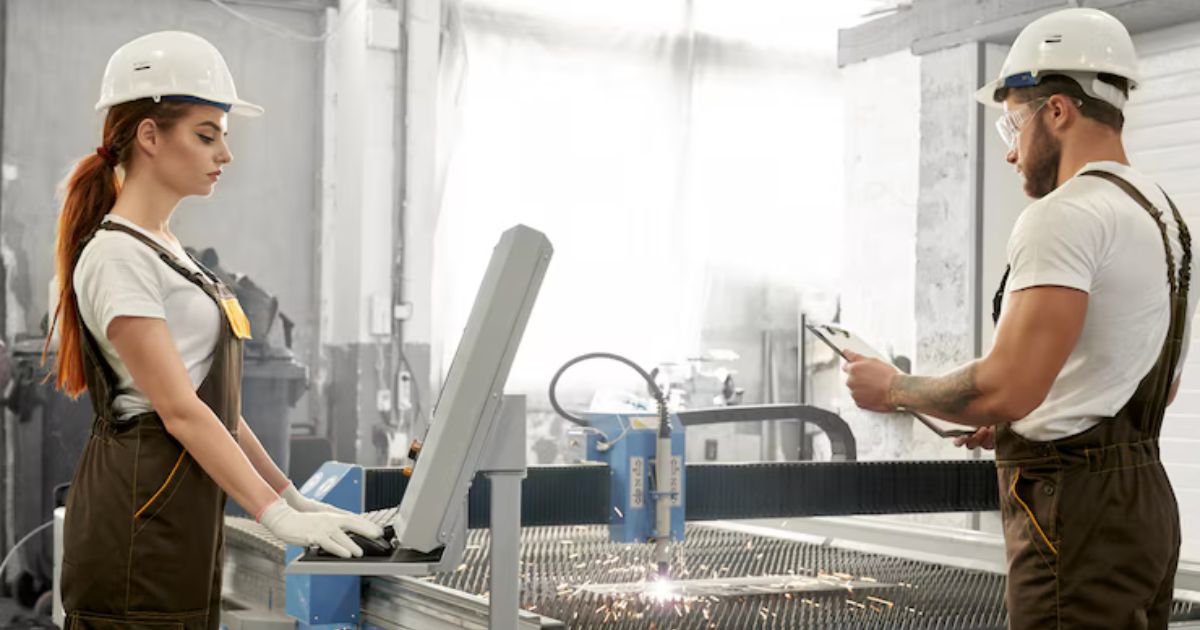
To ensure the best results in metal fabrication, consider the following best practices:
- Regular machine maintenance: Keep your machines in top condition with routine inspections and calibration.
- Material handling: Use automated systems to streamline loading and unloading.
- Employee training: Proper training ensures that workers know how to operate machines effectively, reducing the risk of errors.
- Optimized machine settings: Always ensure that machine settings are adjusted according to the material and thickness to ensure precision.
With Energy Mission’s advanced products, businesses can implement these best practices more effectively, leading to enhanced productivity and profitability.
Conclusion
Metal fabrication is a complex process with numerous challenges, but with the right tools and strategies, businesses can overcome these obstacles and achieve high-quality results. Investing in high-precision, durable, and versatile sheet metal bending machines is key to solving common issues such as inaccurate bends, tool wear, and high operational costs.
Energy Mission’s sheet metal bending machine manufacturing and supplier solutions offer the technology and reliability needed to improve production efficiency and reduce downtime. By choosing the right equipment and following best practices, companies can achieve better outcomes and drive long-term success.