In the world of metal fabrication, one of the most important investments a business can make is in a Sheet metal bending machine. But while the upfront cost may seem like the only factor to consider, the Total Cost of Ownership (TCO) plays a significant role in determining whether that investment is truly worth it in the long run. This blog will break down the TCO of sheet metal bending machines, highlighting the key costs involved and the benefits of making an informed choice when selecting a machine from a reliable sheet metal bending machine manufacturing and supplier.
What is the Total Cost of Ownership (TCO)?
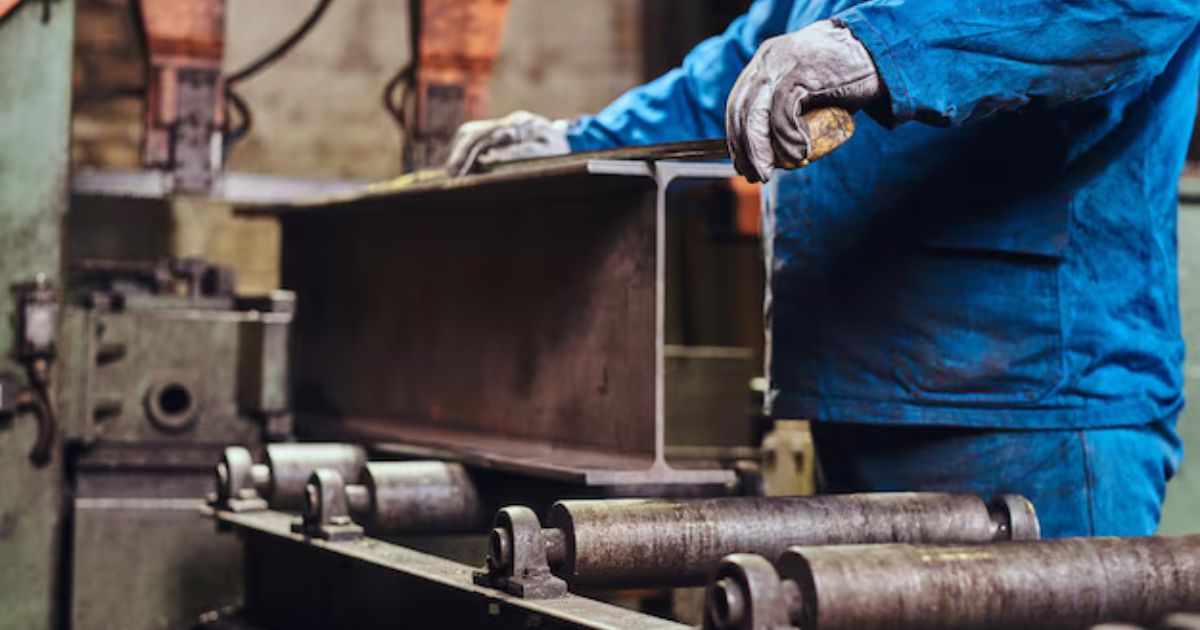
Definition of TCO and Its Relevance in Industrial Investments
The Total Cost of Ownership (TCO) is a comprehensive financial estimate that helps businesses understand not only the upfront cost of acquiring a product, but also the long-term expenses associated with owning and operating it. In industrial settings like sheet metal fabrication, TCO is critical because it accounts for factors such as maintenance, energy usage, repairs, and operational efficiency.
Why TCO is More Significant Than Upfront Costs When Evaluating Sheet Metal Bending Machines
When purchasing a sheet metal bending machine, the initial cost is often the first consideration, but the true cost goes far beyond that. A seemingly affordable machine might come with high operating costs, poor energy efficiency, or costly repairs, making it more expensive over time. By evaluating TCO, businesses can make more informed decisions that optimize long-term profitability.
Importance of Understanding TCO for Sheet Metal Bending Machines
For metal fabrication shops, understanding TCO is crucial to ensure profitability and operational efficiency. Evaluating the TCO of a sheet metal bending machine helps businesses factor in all costs, avoid hidden expenses, and maximize return on investment (ROI). With accurate TCO analysis, you can ensure that the machine you choose will enhance production, reduce costs, and deliver consistent performance over its lifespan.
Key Factors Influencing TCO in Metal Fabrication
Understanding the various components that contribute to TCO is essential for making an informed decision. These factors include everything from upfront purchase costs to maintenance and energy consumption.
1. Components of TCO for Sheet Metal Bending Machines
Upfront Costs
The initial purchase price of a sheet metal bending machine is often the first number to look at. However, many companies fail to consider the costs of customization, tools, and additional accessories that may be necessary to optimize the machine’s use. These can increase the initial investment considerably.
Installation and Setup Costs
Beyond purchasing the machine, setting it up is another crucial cost component. This includes transport and logistics to move the machine to your facility, installation fees, and integration with existing production systems. Additionally, training costs for operators and maintenance staff can add up.
Operational Costs
Operational costs are ongoing expenses related to running the machine. These include energy consumption, which can vary greatly depending on the type of machine you purchase. For instance, electric press brakes tend to have lower energy consumption than hydraulic ones. The cost of consumables, such as lubricants and tools, also plays a significant role in the total operational expenses.
Maintenance and Repair Costs
To keep a sheet metal bending machine operating at peak efficiency, regular maintenance and occasional repairs are necessary. Preventive maintenance is often less costly than reactive repairs, but even with good care, parts like hydraulic seals or CNC components will need to be replaced periodically. Downtime due to machine failures can also significantly affect production schedules and, by extension, costs.
Depreciation
Depreciation refers to the decrease in the value of your sheet metal bending machine over time. It’s important to factor in depreciation when calculating TCO, as the machine will lose value. However, it’s also worth considering the resale value of the machine when you decide to upgrade or sell it.
Opportunity Costs
Opportunity costs account for the losses you might face from downtime or inefficiency caused by older or outdated machines. Comparing advanced machines to older systems reveals the potential gains in productivity and efficiency, which can lead to higher profitability in the long run.
2. Cost-Benefit Analysis
Long-Term Financial Benefits
Investing in high-quality sheet metal bending machines offers several long-term financial benefits. These machines can boost productivity, improve output quality, and reduce material waste due to precision bending. Over time, these advantages lead to significant savings and higher profit margins.
Efficiency Gains
Modern machines offer a host of efficiency benefits. Faster production cycles reduce lead times, and energy-efficient models help reduce utility bills. By automating certain aspects of the bending process, you can also reduce labor costs and human error.
Impact on Profit Margins
Machines that produce higher-quality products can command higher prices in the marketplace. Consistent output from a reliable sheet metal bending machine ensures customer satisfaction, repeat business, and ultimately, better profit margins.
3. Comparing Machine Types Based on TCO
When evaluating the TCO, it’s essential to consider the type of machine you choose. Different machine types come with varying upfront costs, maintenance needs, and energy consumption.
Mechanical Press Brakes
Mechanical press brakes tend to have lower upfront and maintenance costs, but they may not offer the precision and speed of other types. These machines are more suited for general or light-duty operations.
Hydraulic Press Brakes
Hydraulic press brakes are more robust and ideal for heavy-duty operations. While they are moderately priced, their maintenance costs tend to be higher due to the complexities of hydraulic systems. Businesses in industries requiring heavy bending force may find hydraulic press brakes ideal despite their TCO.
Electric Press Brakes
Electric press brakes are known for their energy efficiency, making them an attractive option for businesses aiming to reduce operational costs. Although their upfront costs are higher, they tend to have a lower TCO in the long run due to reduced energy consumption and lower maintenance needs.
CNC Press Brakes
CNC press brakes offer exceptional accuracy and automation, making them the best choice for large-scale operations with a focus on precision. While the initial investment is significant, their efficiency, accuracy, and automation provide substantial long-term savings and a high ROI.
4. Case Studies and Real-World Examples
Small-Scale Fabrication Shop
For a small fabrication shop, the decision to purchase a sheet metal bending machine often hinges on balancing upfront costs with long-term benefits. A case study of a mid-range hydraulic press brake illustrates how businesses with limited capital can still make smart investments by understanding the full scope of TCO.
Large Industrial Manufacturer
Large manufacturers that rely on high-volume production can justify the purchase of CNC press brakes, despite their higher upfront cost, due to long-term savings from efficiency gains and energy reduction.
Cost Comparisons Across Industries
The TCO for sheet metal bending machines differs across industries. For instance, the automotive sector may prioritize precision and automation, while the construction industry may need durable, heavy-duty machines. A detailed comparison shows how different sheet metal bending machine manufacturers and suppliers cater to industry-specific needs.
5. The Role of a Reliable Supplier in Managing TCO
Supplier Expertise
A knowledgeable supplier can guide you in selecting the right sheet metal bending machine for your needs. By considering factors such as energy efficiency, durability, and machine specifications, an expert can help minimize your TCO.
After-Sales Support
The value of after-sales support cannot be overstated. Warranties, maintenance packages, and prompt access to spare parts from a trusted sheet metal bending machine supplier can drastically reduce downtime and repair costs.
Technological Upgrades
Choosing a supplier that offers retrofit and upgrade services ensures that your machine remains at the cutting edge, reducing the need for costly replacements and helping you minimize TCO.
Spotlight: Energy Mission
Energy Mission, a leading sheet metal bending machine manufacturer and supplier, provides solutions that reduce TCO through energy-efficient designs and long-lasting machinery. With their advanced features, businesses can expect improved operational costs and ROI.
6. Steps to Evaluate and Minimize TCO
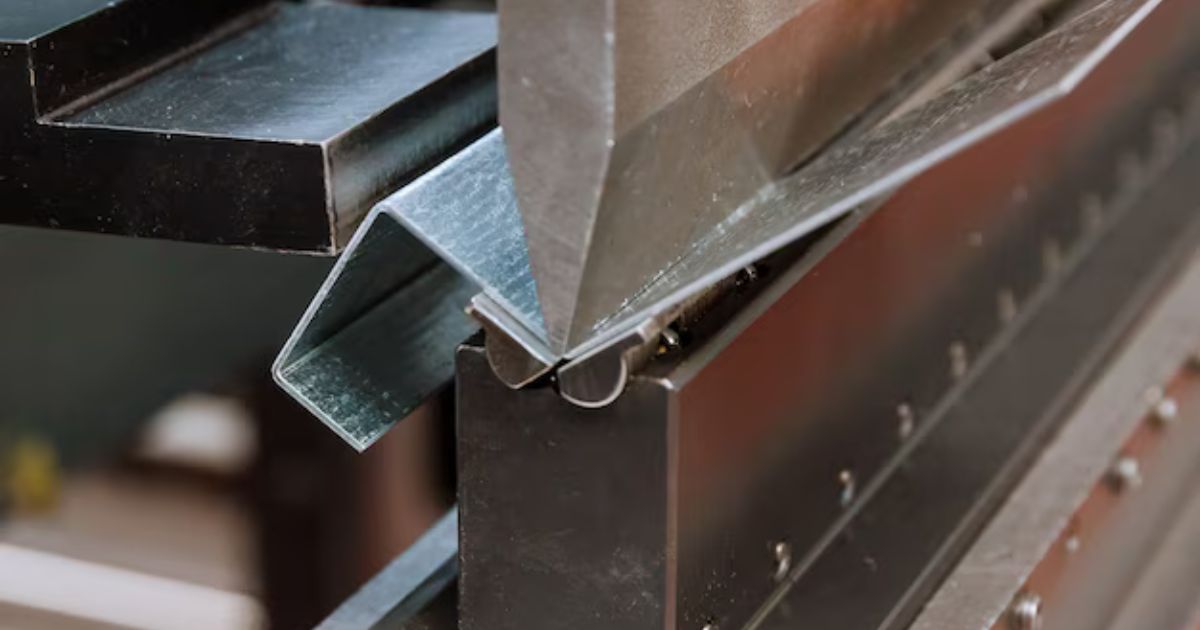
Conducting a Detailed TCO Analysis
To ensure that you choose the best machine for your business, a thorough TCO analysis is essential. This involves checking all cost components and using tools to calculate long-term expenses associated with the machine.
Optimizing Machine Usage
Maximizing the efficiency of your sheet metal bending machine involves implementing regular maintenance schedules and training operators to minimize errors and enhance productivity.
Planning for Future Expansion
Investing in scalable machines that can grow with your business is another crucial aspect of minimizing TCO. Modular designs or machines with upgrade options are a smart choice for companies with plans to expand.
7. Future Trends in Sheet Metal Bending Machines
Innovations Driving Down TCO
Emerging technologies like AI-assisted CNC systems and advanced automation are expected to drive down TCO by improving efficiency and reducing human intervention in the bending process.
The Push Towards Sustainability
Sustainability is a growing trend, with many sheet metal bending machine manufacturers focusing on developing energy-efficient, environmentally friendly machines to reduce operational costs and carbon footprints.
Conclusion
The Total Cost of Ownership is a crucial metric for evaluating sheet metal bending machine manufacturing and supplier options. By considering long-term costs, including energy use, maintenance, and depreciation, businesses can make informed choices that lead to greater profitability. Investing in high-quality, efficient, and durable machines will maximize ROI, while partnering with reliable suppliers ensures you’re well-equipped to manage TCO for years to come.