CNC Press Brake Machines are revolutionizing metal fabrication by combining precision, efficiency, and versatility. Whether producing automotive parts, aerospace components, or structural elements for construction, these machines have become essential in modern manufacturing. This comprehensive guide delves deep into the workings, benefits, applications, and future trends of CNC Press Brake Machines to help you understand their significance.
What is a CNC Press Brake Machine?
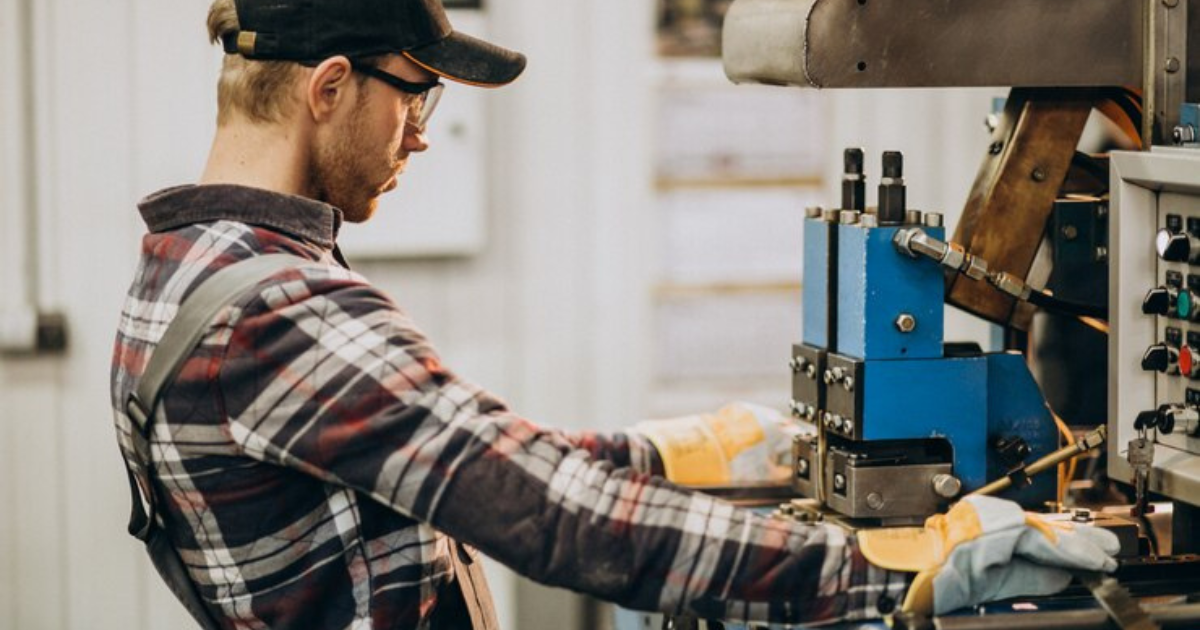
A CNC (Computer Numerical Control) Press Brake Machine is a metalworking tool designed to bend sheet and plate metals into custom shapes. Unlike traditional press brake machines that require manual adjustments, CNC versions use advanced software to automate and optimize the bending process.
Imagine shaping a piece of metal with the precision of a sculptor but at the speed of a high-tech machine. CNC Press Brake Machines deliver unparalleled accuracy, making them ideal for mass production and complex designs.
Why CNC Machines Are Better Than Traditional Press Brakes
- Precision: CNC machines calculate exact angles and pressures, minimizing errors.
- Efficiency: Automation reduces setup times and allows for continuous production.
- Flexibility: These machines can handle a variety of designs, from simple folds to intricate patterns.
The Importance of CNC Press Brake Machines in Manufacturing
CNC Press Brake Machines are at the heart of modern manufacturing, offering solutions to meet the growing demand for precision and scalability. Their role spans multiple industries:
- Automotive: From lightweight panels to intricate chassis parts, these machines enable consistent production.
- Aerospace: They manufacture parts that meet stringent safety and performance standards.
- Construction: They create structural elements like beams and decorative pieces with speed and accuracy.
In industries where quality and consistency can mean the difference between success and failure, CNC Press Brake Machines are indispensable.
How CNC Technology Enhances Press Brake Machines
CNC technology transforms traditional press brakes into smart machines capable of precise and automated operations. By integrating software and mechanical systems, CNC machines take the guesswork out of bending.
How It Works
- Input the Design: The operator uploads a CAD (Computer-Aided Design) file.
- Machine Calibration: CNC software calculates the required force, angle, and sequence for each bend.
- Execution: The press brake uses this data to deliver precise bends, every time.
The automation ensures consistency across production batches and reduces material wastage.
Key Components of a CNC Press Brake Machine
A CNC Press Brake Machine is a blend of advanced hardware and software. Let’s break down its main components:
1. Control Unit
The control unit is the brain of the machine. It interprets CAD files and provides instructions for the bending process. Modern control units often feature touchscreens, making them user-friendly.
2. Hydraulic System
The hydraulic system provides the force needed to bend the metal. It uses pressurized fluid to move the punch and die with precision.
3. Punch and Die
These tools shape the metal. The punch presses the metal into the die, which determines the angle and form of the bend.
4. Back Gauge
This component positions the metal sheet accurately before bending, ensuring consistent results.
5. Safety Features
Modern machines include safety elements like light curtains and emergency stops to protect operators.
How Does a CNC Press Brake Machine Work?
Operating a CNC Press Brake Machine involves the following steps:
-
-
- Design Creation: The operator designs the part using CAD software.
- Upload: The design is uploaded to the machine’s control unit.
- Material Setup: The metal sheet is placed between the punch and die.
- Calibration: The machine calculates the bending parameters.
- Bending: The press brake applies force to create the desired shape.This streamlined process reduces errors and improves production speed.
-
Types of CNC Press Brake Machines
There are three primary types of CNC Press Brake Machines, each designed for specific applications:
1. Hydraulic CNC Press Brake Machines
-
-
- Best For: Heavy-duty bending tasks.
- Pros: High power and reliability.
- Cons: Higher energy consumption.
-
2. Electric CNC Press Brake Machines
-
-
- Best For: Precision tasks and environmentally friendly operations.
- Pros: Energy-efficient and quieter.
- Cons: Limited to lighter materials.
-
3. Hybrid CNC Press Brake Machines
-
-
- Best For: A balance of power and efficiency.
- Pros: Combines hydraulic strength with electric efficiency.
- Cons: Typically more expensive.
-
Benefits of CNC Press Brake Machines
The advantages of CNC Press Brake Machines go beyond precision and automation. Let’s explore their broader impact:
-
Superior Precision
The integration of CNC technology ensures each bend meets exact specifications. This is crucial in industries like aerospace, where even minor deviations can compromise safety.
-
Enhanced Productivity
CNC machines can produce large quantities of components in a fraction of the time it takes traditional machines. Automated operations reduce setup times and enable round-the-clock production.
-
Cost Efficiency
By minimizing material waste and improving production speeds, CNC Press Brake Machines lower operational costs. Energy-efficient models also reduce utility expenses.
-
Versatility
From simple brackets to complex parts, CNC machines handle diverse projects. Their flexibility supports various industries, including automotive, construction, and manufacturing.
Applications of CNC Press Brake Machines
CNC Press Brake Machines are vital across numerous sectors. Here’s a closer look at their applications:
1. Automotive Industry
-
-
- Parts Produced: Car panels, brackets, chassis components.
- Why They Matter: Precision ensures safety and aesthetic appeal.
-
2. Aerospace Industry
-
-
- Parts Produced: Fuselage sections, wing panels, brackets.
- Why They Matter: Components must meet rigorous quality standards.
-
3. Construction Industry
-
-
- Parts Produced: Beams, decorative panels, structural supports.
- Why They Matter: CNC machines enable customized designs and durability.
-
Other Applications
-
-
- Electrical enclosures.
- HVAC ducting.
- Custom brackets for machinery.
-
How to Choose the Right CNC Press Brake Machine
When investing in a CNC Press Brake Machine, consider the following factors:
-
Production Requirements
Match the machine’s tonnage and bending length to your production needs. A heavy-duty Hydraulic model may be necessary for thicker materials, while an electric machine suffices for lightweight tasks.
-
Software Features
Look for advanced control units that support CAD integration and real-time monitoring.
-
Maintenance Needs
Machines with minimal maintenance requirements reduce downtime and long-term costs.
-
Brand Reputation
Top brands like Amada, Trumpf, and Bystronic offer reliable machines with excellent customer support.
Best Practices for Operating a CNC Press Brake Machine
-
-
- Prioritize Safety: Always wear protective gear and ensure safety systems, like light curtains and emergency stops, are operational. Proper training for operators is essential.
- Regular Maintenance: Routine checks on hydraulic systems, punches, and dies extend the machine’s lifespan and maintain its performance.
- Optimize Programming: Use CAD software to create accurate designs and test programs on scrap material before large production runs.
-
Innovations in CNC Press Brake Technology
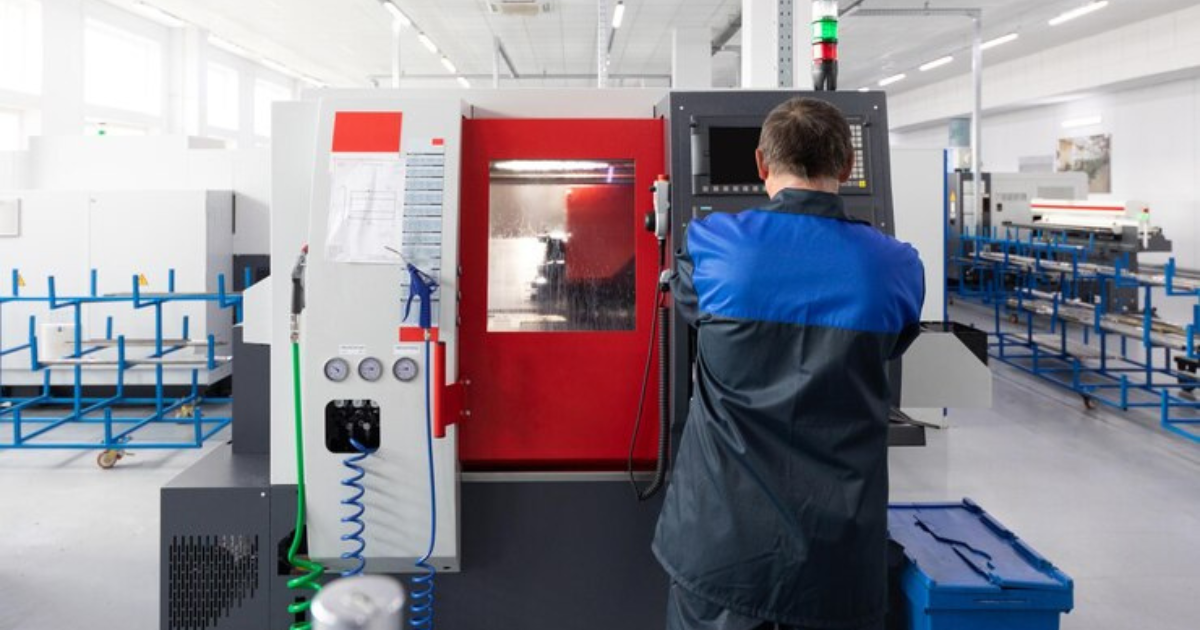
CNC Press Brake Machines are continually evolving. Here are some recent advancements:
-
-
- AI Integration : Artificial Intelligence enhances efficiency by analyzing data to optimize bending sequences and reduce errors.
- Real-Time Monitoring: Operators can now track machine performance and detect issues early, minimizing downtime.
- Robotics Integration: Robots are increasingly paired with CNC machines to automate material handling, further improving productivity.
-
The Future of CNC Press Brake Machines
As technology advances, CNC Press Brake Machines are becoming smarter and more efficient. Innovations like fully autonomous systems and enhanced material handling capabilities are on the horizon. These developments promise to reshape the manufacturing landscape.
Conclusion
CNC Press Brake Machines have transformed metal fabrication, offering unmatched precision, efficiency, and versatility. Their role in industries like automotive, aerospace, and construction underscores their importance in modern manufacturing. By embracing these machines, manufacturers can achieve high-quality results while reducing costs and lead times.