In industries such as aerospace, automotive, and electronics, precision metalworking is crucial to ensure the highest quality products with exact specifications. Achieving this level of precision requires reliable, advanced machinery capable of handling complex tasks without compromise. The SPLENDID Series CNC Press Brake stands out as one of the top choices for manufacturers who demand the highest standards of accuracy and consistency.
In this article, we’ll explore the key features of the SPLENDID Series CNC Press Brake and discuss why it’s the ideal solution for precision metalworking applications.
1. Unmatched Precision in Bending and Forming
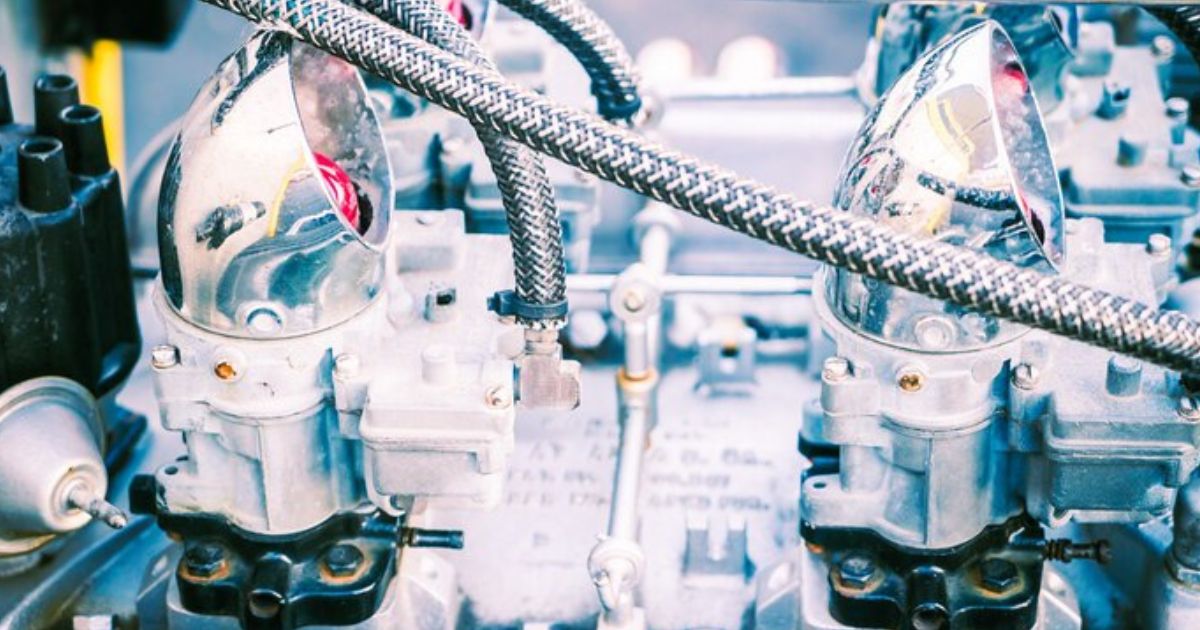
The core strength of the SPLENDID Series CNC Press Brake lies in its ability to provide exceptional precision during every stage of the bending and forming process. This is essential for industries where small deviations can result in product defects or costly rework.
Advanced Control Systems for Accuracy
At the heart of the SPLENDID Series is its state-of-the-art CNC control system. These controls allow operators to program and monitor each bending operation with high precision, ensuring that every bend is executed according to the exact specifications.
Key features contributing to precision:
- High-Resolution Feedback Systems: The SPLENDID Series uses advanced encoders and feedback loops to monitor the position of the ram and backgauge. This feedback ensures that the machine’s movements are highly accurate, even at high speeds.
- Touchscreen Interface: The intuitive touchscreen interface allows for quick setup and fine-tuning of parameters, ensuring that every bending process is completed with the utmost precision.
2. Superior Material Handling Capabilities
The SPLENDID Series CNC Press Brake is engineered to handle a wide range of materials with varying thicknesses and properties, making it versatile for diverse applications. For precision metalworking, this means the machine can consistently handle complex tasks without sacrificing accuracy, regardless of the material being used.
Adaptable to Different Material Types
Whether you are working with thin sheets of aluminum or thicker stainless steel, the SPLENDID Series provides the necessary power and flexibility to bend various materials with high precision.
Materials commonly processed by the SPLENDID Series:
- Aluminum: Softer and lightweight, requiring precise control to avoid material distortion.
- Mild Steel: Commonly used in industrial applications, demanding accurate bends to ensure structural integrity.
- Stainless Steel: Known for its strength and durability, stainless steel requires advanced control systems to maintain accuracy during bending.
Bending Thick and Thin Sheets with Equal Precision
Whether dealing with thin-gauge materials or thicker gauges, the SPLENDID Series CNC Press Brake ensures that every bend is made with high precision. Its tonnage capabilities and the adjustable pressure system allow for uniform bending across varying material thicknesses.
3. Intelligent Backgauge and Crowning Systems
To achieve precise bending, especially for long and complex parts, the backgauge and crowning systems in the SPLENDID Series are critical. These systems ensure that the material remains securely positioned and that the force is evenly distributed across the entire sheet.
Backgauge Precision
The backgauge is designed to position the sheet metal accurately before each bend. This ensures that the bending process is uniform across the material, preventing errors in positioning that can lead to bent parts that are out of spec.
- Automatic Backgauge Adjustment: The backgauge can automatically adjust for different material sizes and bending angles, ensuring constant precision during high-speed production runs.
- Multiple-Axis Control: The SPLENDID Series offers multi-axis backgauge systems that allow for more complicated bending patterns while maintaining tight tolerances.
Crowning System for Even Bends
The crowning system ensures that the sheet is bent uniformly along its entire length. As press brakes operate, the tonnage applied can cause slight deflection in the machine’s ram, but the crowning system compensates for this, ensuring the correct angle is achieved.
- Automatic Crowning Adjustment: The crowning system adjusts itself automatically to compensate for any deformation, especially during longer bending processes, to maintain accurate results.
4. Enhanced Workflow with Automation and Customization
In the fast-paced world of precision metalworking, automation plays a crucial role in maintaining consistent results and minimizing human error. The SPLENDID Series CNC Press Brake is equipped with several automation features that make it easier to operate while ensuring consistent accuracy across all operations.
Automatic Tool Changing System
The automatic tool changer reduces setup time and minimizes errors by automatically selecting the correct tooling for the specific operation. This feature is especially valuable for manufacturers who frequently work with different materials and require frequent tool changes.
- Reduced Downtime: The automatic tool changer reduces the time it takes to switch between tools, increasing overall productivity.
- Increased Accuracy: With fewer manual adjustments, the chances of errors in tooling are reduced, improving overall accuracy in the bending process.
Integrated Software for Precise Programming
The SPLENDID Series comes with powerful software that allows for easy programming and integration with other automated systems in the factory. The software includes pre-set bending parameters for various materials and thicknesses, reducing the chances of human error and ensuring consistent precision throughout production runs.
5. Consistency in High-Volume Production
For high-volume manufacturers, consistency is just as important as precision. The SPLENDID Series is designed to maintain consistent results over long production runs, making it ideal for industries where quality control and uniformity are critical.
High-Speed, High-Precision Performance
Thanks to its advanced CNC controls and automated systems, the SPLENDID Series can produce high-precision parts at high speeds without sacrificing quality. This is particularly beneficial for industries like automotive manufacturing, where large quantities of parts must be produced to exact specifications.
- Consistency in Repetitive Bending: The machine’s ability to maintain consistent bending angles and material handling capabilities ensures that each part is produced to exact specifications, even in high-volume runs.
- Long-Term Durability: The SPLENDID Series is built to withstand heavy usage without degradation in performance, making it a reliable choice for consistent results over time.
6. Easy Maintenance and Longevity
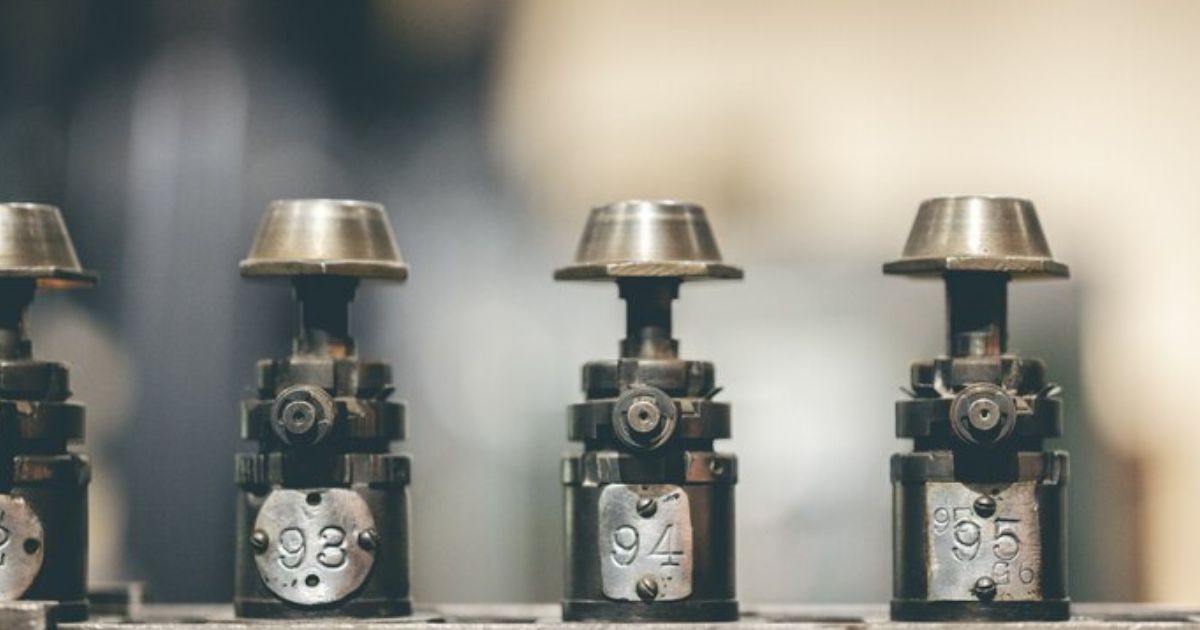
The SPLENDID Series CNC Press Brake is designed for easy maintenance, ensuring that the machine remains operational and precise throughout its long service life.
Self-Diagnosis and Monitoring Systems
The machine includes self-diagnostic features that monitor the performance of various components in real-time. If a problem arises, the system alerts the operator, helping to minimize downtime and prevent costly repairs.
- Easy Access to Components: With a well-designed structure, components like the ram and hydraulic systems are easily accessible for routine maintenance.
- Longer Service Life: Regular maintenance and the robust construction of the SPLENDID Series ensure that the press brake can operate for years without losing its precision.
Conclusion
The SPLENDID Series CNC Press Brake is an outstanding choice for industries that require high-precision metalworking. Its combination of advanced control systems, automated features, versatile material handling, and long-term durability makes it ideal for businesses looking to produce high-quality metal parts with minimal errors and maximum efficiency. Whether you are working with thin sheets of aluminum or thicker steel, the SPLENDID Series ensures that each bend is executed with precision, consistency, and reliability.
By incorporating the SPLENDID Series CNC Press Brake into your production process, you can not only meet the highest standards of accuracy but also improve overall productivity, reduce downtime, and enhance the quality of your products.