When operating a metal fabrication business, selecting the appropriate sheet metal bending machine is one of the most critical decisions you’ll make. This machine will affect the precision, speed, and quality of your products. Moreover, it directly influences the overall efficiency, safety, and profitability of your operations. From small-scale operations to large industrial fabrication facilities, understanding the different types of bending machines and their features is essential for making a sound investment.
In this guide, we’ll break down the various factors to consider when purchasing a sheet metal bending machine, helping you make a decision that aligns with your business goals and production needs.
Understanding Sheet Metal Bending Machines
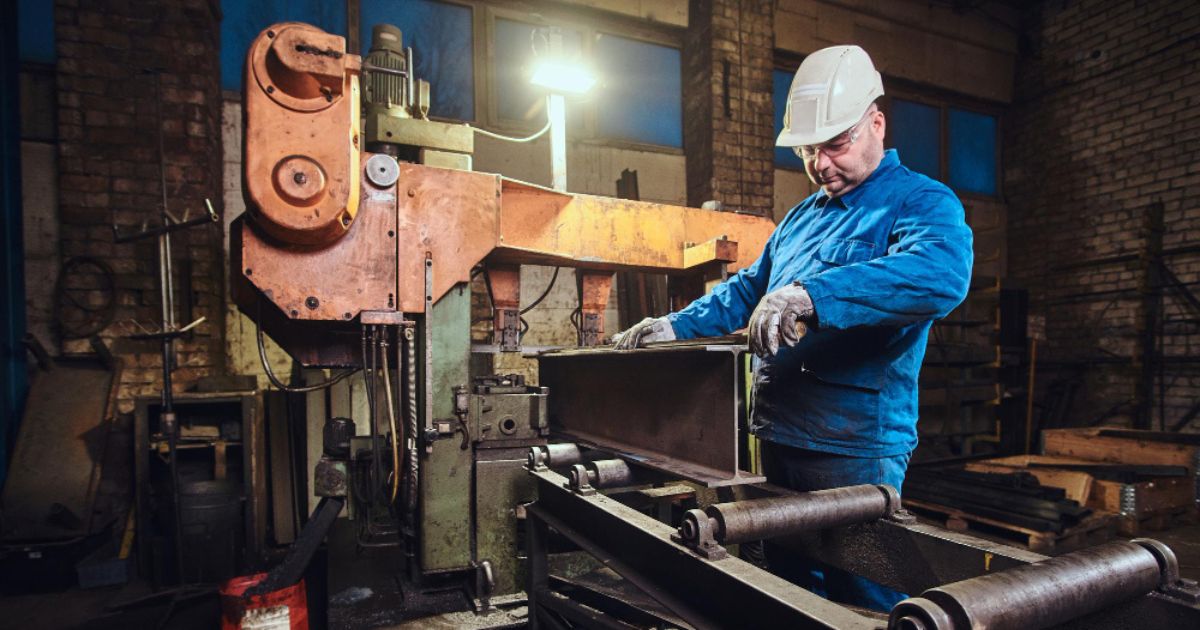
At its core, a sheet metal bending machine (often referred to as a press brake) is a piece of equipment designed to shape metal sheets into specific forms, typically by bending them at precise angles. These machines are widely used in industries such as automotive, aerospace, construction, and manufacturing to create a variety of metal products, including brackets, frames, and custom parts.
Bending machines come in a range of types, sizes, and capabilities, and choosing the right one requires a solid understanding of your business needs, as well as the machine’s capabilities and limitations. Sheet metal bending machines can be classified based on their operation method, control systems, and mechanical configurations. Below, we will delve deeper into the different types of bending machines available and discuss how to determine which one is best suited to your specific applications.
Types of Sheet Metal Bending Machines
- Mechanical Press Brakes
- These are simple and cost-effective options suitable for basic bending tasks. They operate using a mechanical system that transmits force to the tool.
- Advantages: Lower initial cost, faster cycle time, and simplicity of operation.
- Disadvantages: Limited precision and flexibility.
- Hydraulic Press Brakes
- Hydraulic press brakes are widely used in modern fabrication due to their versatility and precision. They use hydraulic systems to apply force, making them more adaptable to different materials and bending tasks.
- Advantages: Higher bending accuracy, ability to handle thicker materials, and smooth operation.
- Disadvantages: Higher upfront costs, more complex maintenance.
- Energy Mission’s Hydraulic Press Brakes are an excellent example of such machines, offering a combination of strength and efficiency for larger jobs.
- CNC Press Brakes
- These machines are equipped with computer numerical control (CNC) systems, offering advanced features for automated operations, enhanced precision, and repeatability.
- Advantages: Precision, repeatability, and the ability to handle complex designs with minimal human intervention.
- Disadvantages: Higher cost, specialized training required for operators.
- Discover our CNC Press Brake Machines, designed to meet the high-demand needs of modern fabrication businesses.
- Electric Press Brakes
- Electric press brakes provide energy-efficient alternatives to hydraulic systems. They rely on electric motors for power transmission.
- Advantages: Reduced energy consumption, lower operational costs, and faster cycle times.
- Disadvantages: Limited bending power compared to hydraulic presses.
Key Factors to Consider When Choosing a Sheet Metal Bending Machine
- Type of Material Different bending machines are designed to handle specific materials. Factors like material thickness, hardness, and flexibility play a vital role in determining the best machine for your business.
- For instance, if you often work with thick sheets of steel, you’ll need a machine capable of providing significant bending force, such as a hydraulic or CNC press brake
- Material Thickness and Size The thickness and size of the materials you need to bend will determine the force capacity of the machine. Machines have specific bending capacities, so you must ensure that the one you choose can handle your maximum material thickness.
- Thinner materials (up to 6mm): Mechanical press brakes are often sufficient.
- Thicker materials (over 6mm): Hydraulic or CNC machines are more suitable due to their higher capacity.
- Accuracy and Precision Requirements The level of precision needed for your work is a crucial consideration when choosing a machine. If your business requires high precision for intricate bends or complex designs, a CNC press brake would be an ideal choice.
- Look for machines with backgauges, which help position the material accurately before bending, ensuring uniform results.
- Tolerance: Machines with tighter tolerances are necessary for applications where exact angles are critical.
- Automation and Software Integration
- CNC Integration: If you’re looking for a machine that can handle high-volume production with minimal manual input, investing in a CNC press brake might be worthwhile. These systems are equipped with advanced software that automates complex tasks and enhances productivity.
- Automation Benefits: Reduced operator intervention, more consistent results, and faster turnaround times.
- Programming Software: Look for machines that come with easy-to-use programming interfaces and software for designing custom bends.
- Power and Speed
- The power requirements of your machine will depend on the type of materials you’re processing and the complexity of your work.
- For high-volume production, look for machines that offer both speed and accuracy. However, don’t sacrifice quality for speed; ensure that the machine’s capacity aligns with your production demands.
- Consider the bending speed (how quickly the machine completes each cycle) and force capacity (how much force the machine can apply to bend materials).
- Safety Features Industrial machinery poses safety risks, so it’s essential to choose a machine with adequate safety features to protect workers.
- Features such as light curtains, safety sensors, and emergency stops are critical for preventing accidents.
- Ensure that the machine complies with local safety regulations and offers easy access to maintenance points.
- Space and Installation Considerations Sheet metal bending machines can be large, requiring significant space for installation. Before purchasing, measure your shop floor and ensure there’s sufficient room for the machine and its required operational space.
- Consider additional space for tooling, material handling equipment, and operator safety zones.
- Installation services are usually provided by suppliers, but make sure to account for these costs in your overall budget.
Supplier Selection: Why It Matters
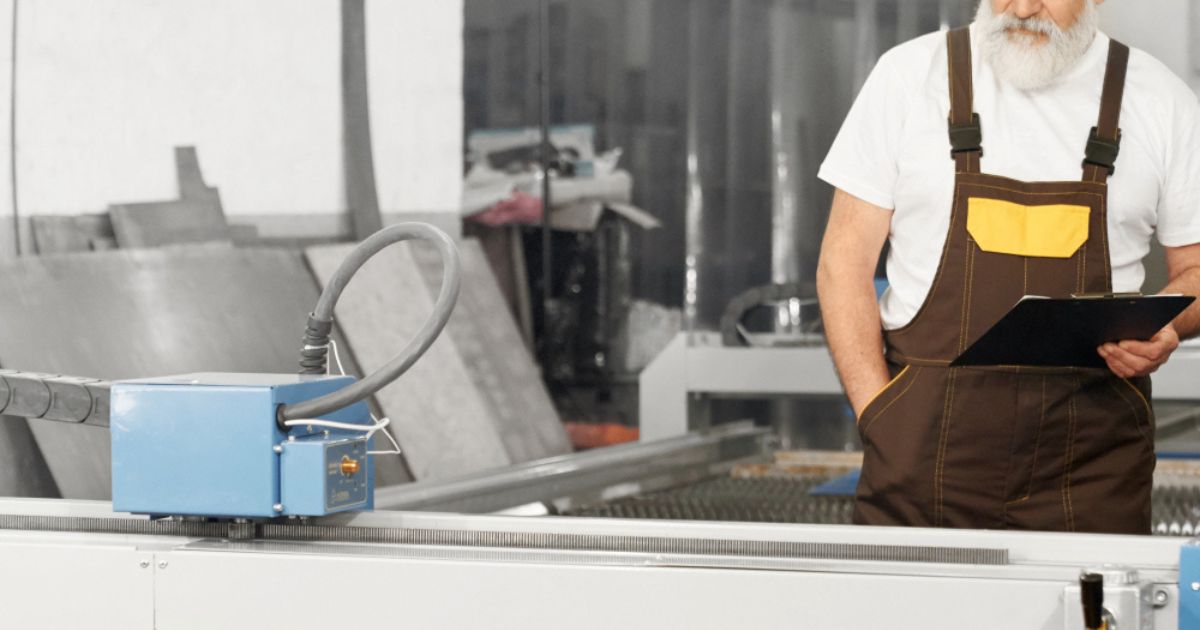
Choosing the right supplier is just as important as selecting the right machine. The reputation and support provided by a supplier can significantly impact your business operations.
- Product Quality and Reputation
- Look for a supplier known for providing high-quality, durable machines. Research reviews, ask for references, and check the supplier’s track record in the industry.
- Ensure that the supplier offers machines built to last and capable of handling your specific requirements.
- After-Sales Support
- A reliable supplier should offer comprehensive after-sales support, including installation assistance, operator training, and ongoing maintenance services.
- Consider the availability of spare parts and the supplier’s response time to ensure minimal downtime in case of issues.
- Warranty and Service Packages
- Always choose a supplier that offers warranties and service packages. A solid warranty shows the supplier’s confidence in their product and provides peace of mind in case of defects.
- Maintenance packages can extend the machine’s lifespan, keeping it in top working condition.
- Customization and Flexibility
- A good supplier will offer customization options for machines, allowing you to tailor the equipment to your specific needs. This is particularly important for businesses that require specialized bending tasks or have unique material types.
Calculating the Total Cost of Ownership (TCO)
When evaluating sheet metal bending machines, consider not just the initial purchase price but also the total cost of ownership (TCO) over the machine’s lifetime. This includes:
- Upfront Costs: The initial purchase price of the machine, including any customization or special features.
- Operational Costs: Energy consumption, consumables, and tools required for operation.
- Maintenance and Repairs: Ongoing service costs, including periodic maintenance, parts replacement, and any downtime costs.
- Depreciation: The loss of machine value over time, especially if it’s used extensively.
By calculating the TCO, you can better understand the financial commitment required and choose the machine that offers the best long-term value.
Conclusion
Choosing the right sheet metal bending machine is an essential decision that will impact your business’s productivity, efficiency, and profitability. By carefully considering the material requirements, accuracy needs, machine type, and supplier options, you can select the perfect machine for your operations. Always ensure you’re partnering with a reliable supplier who offers top-notch support and service. Remember, the right machine isn’t just the one with the best price – it’s the one that fits your business’s unique needs and drives long-term success.