In today’s fast-evolving industrial landscape, CNC press brake machines have emerged as a cornerstone of modern manufacturing. With their precision, efficiency, and versatility, these machines are revolutionizing sheet metal fabrication across various industries, including automotive, aerospace, construction, and energy. The demand for CNC press brake machines is surging, creating opportunities and challenges for manufacturers looking to stay ahead in a competitive market.
This article delves into the factors driving the growing demand for CNC press brake machines, explores the latest trends, and provides actionable insights for manufacturers to capitalize on this upward trajectory.
What Is Driving the Demand for CNC Press Brake Machines?
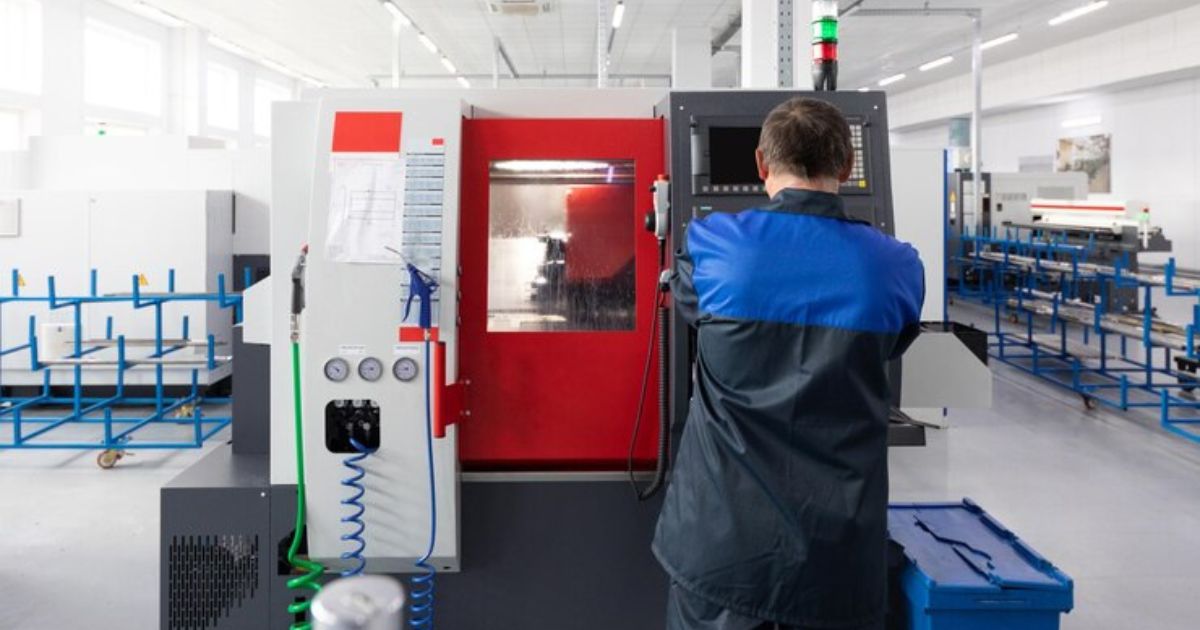
Precision and Efficiency in Sheet Metal Fabrication
One of the primary reasons behind the growing demand is the unmatched precision and efficiency offered by CNC press brake machines. Traditional bending methods often struggle with maintaining consistency, especially in high-volume production. CNC machines, on the other hand, ensure consistent accuracy, faster production, and reduced waste by minimizing errors and optimizing operations.
For manufacturers, these benefits translate into improved productivity and cost savings. The ability to program precise specifications and repeat them with minimal variation ensures a level of reliability that traditional methods cannot match. This precision also allows manufacturers to meet the increasingly stringent quality standards set by various industries.
Rising Demand Across Key Industries
CNC press brake machines are indispensable in industries requiring complex and high-quality sheet metal components. Key sectors fueling this demand include:
- Automotive: Lightweight and durable components are essential for enhancing fuel efficiency and safety.
- Aerospace: High-precision parts are critical for maintaining safety and performance.
- Energy: Renewable energy projects, such as wind turbines, depend on precision-engineered components.
As these industries continue to grow and innovate, the demand for CNC press brake machines is expected to follow suit.
Technological Advancements
Modern CNC press brake machines feature innovations like IoT integration, automated tool changers, and user-friendly interfaces. These advancements enhance productivity while reducing labor costs and maintenance requirements, making them an attractive investment for manufacturers.
IoT-enabled machines provide real-time monitoring and predictive maintenance capabilities, minimizing downtime and improving operational efficiency. Automated tool changers reduce setup times, allowing for quicker transitions between production runs. Such features enable manufacturers to meet tight deadlines and respond swiftly to changing customer demands.
Focus on Sustainability
With sustainability becoming a priority, CNC press brake machines align with green manufacturing goals. Their energy efficiency and low material wastage contribute to eco-friendly production processes. Unlike traditional methods, which often involve significant waste, CNC machines optimize material usage, reducing the environmental impact of manufacturing activities.
Key Trends Shaping the CNC Press Brake Market
Automation and Robotics
The integration of automation and robotics is transforming the CNC press brake industry. Collaborative robots, or cobots, assist with material handling, improve safety, and enhance operational efficiency. These advancements enable manufacturers to achieve higher throughput with fewer manual interventions, reducing the risk of human error.
Automated solutions also allow for continuous production, even in 24/7 operations, ensuring that manufacturers can meet the demands of high-volume orders without compromising quality.
Customization Capabilities
Manufacturers are demanding machines capable of handling diverse materials and designs. Customizable CNC press brake machines, with adjustable bending angles and modular designs, cater to these evolving needs. These machines allow manufacturers to produce a wide range of products, from intricate designs to large-scale components, with ease.
Customization also extends to software capabilities, enabling manufacturers to integrate their CNC machines seamlessly into existing workflows and production systems.
Regional Growth Trends
The Asia-Pacific region is experiencing rapid growth in CNC press brake adoption due to industrialization, government initiatives, and cost-effective labor markets. Countries like China, India, and Vietnam are investing heavily in advanced manufacturing technologies to boost their global competitiveness.
Meanwhile, established markets in North America and Europe continue to innovate and lead. These regions prioritize high-quality output and advanced automation, setting benchmarks for other markets to follow.
Electric Press Brakes on the Rise
Electric CNC press brake machines are gaining popularity for their precision, low maintenance, and energy efficiency. Unlike hydraulic machines, electric press brakes offer smoother operations and better control over bending processes. These machines cater to manufacturers looking to optimize operational costs while maintaining high-quality output.
Benefits of CNC Press Brake Machines for Manufacturers
Enhanced Productivity
Automated operations allow manufacturers to handle large-scale projects efficiently. Faster setup times and precise programming enable quicker deliveries and higher output. This increased productivity ensures that manufacturers can take on more projects and meet tight deadlines without compromising quality.
Cost Savings
Accurate bending minimizes material wastage, while automation reduces labor costs. Additionally, the energy-efficient operation of modern machines further contributes to cost reduction. Over time, these savings can offset the initial investment, making CNC press brake machines a cost-effective solution for manufacturers.
Improved Quality and Reliability
CNC press brake machines ensure uniformity across production runs, building customer trust and enhancing brand reputation through consistent quality. Reliable performance also reduces the likelihood of defects, ensuring that end products meet or exceed customer expectations.
Challenges for Manufacturers and How to Overcome Them
High Initial Investment
Although CNC press brake machines require significant upfront costs, manufacturers can mitigate this through leasing options and by focusing on long-term returns. The productivity gains and cost savings often justify the investment. Additionally, governments and financial institutions in some regions offer subsidies or low-interest loans to support the adoption of advanced manufacturing technologies.
Skilled Labor Shortage
Training programs and investments in user-friendly CNC machines can address the challenge of a limited skilled workforce. Simplified interfaces and automation reduce the reliance on highly trained operators. Manufacturers can also collaborate with technical institutes to develop tailored training programs, ensuring a steady supply of skilled labor.
Staying Competitive
To stand out, manufacturers should prioritize after-sales support, offer tailored solutions, and stay ahead with innovative features. Continuous improvement and customer focus can drive competitiveness. Establishing strong relationships with customers through personalized services and proactive communication can also foster loyalty and repeat business.
Actionable Insights for CNC Press Brake Machine Manufacturers
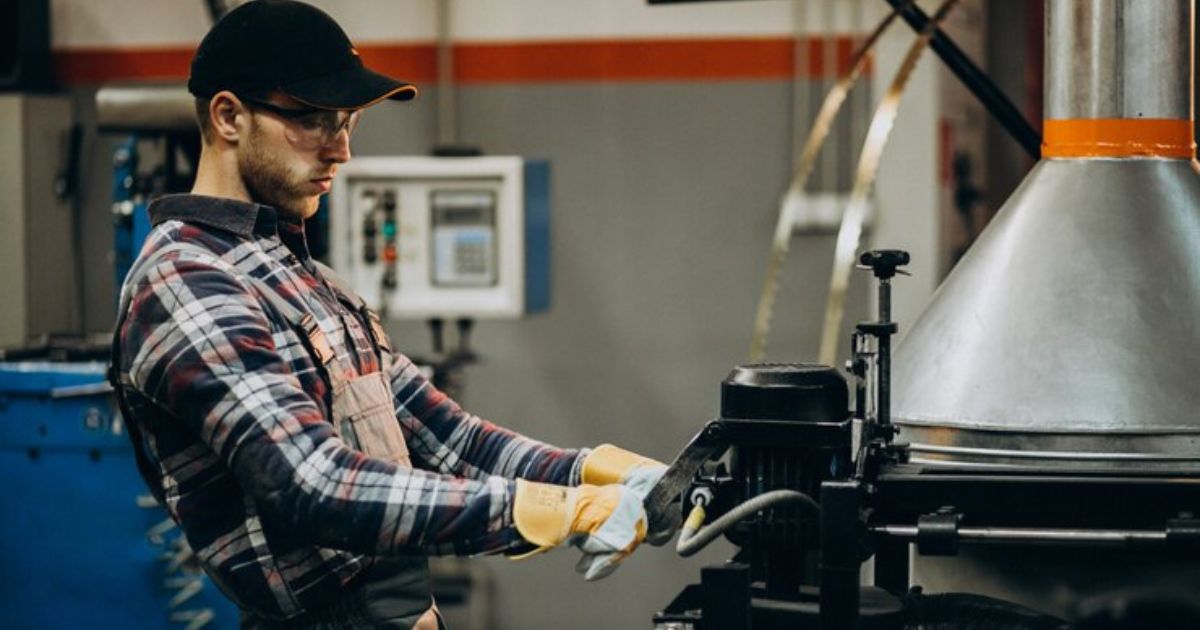
Embrace Digital Transformation
Incorporate technologies like IoT and AI to enhance machine performance and decision-making. Predictive maintenance and real-time monitoring can optimize operations and minimize downtime. By leveraging data analytics, manufacturers can gain valuable insights into production trends and identify areas for improvement.
Focus on Customer-Centric Solutions
Understanding customer needs and offering tailored services—from flexible financing to comprehensive training—can build loyalty and long-term partnerships. Providing value-added services, such as custom machine configurations and responsive technical support, can further differentiate manufacturers from competitors.
Expand Market Reach
Entering new markets and diversifying offerings can unlock growth opportunities. Collaborate with local distributors or establish partnerships to gain traction in emerging regions. Participating in trade shows and leveraging digital marketing can also help manufacturers showcase their products to a broader audience.
Conclusion
The growing demand for CNC press brake machines presents immense opportunities for manufacturers ready to adapt to evolving market demands. By embracing technological advancements, focusing on sustainability, and delivering customer-centric solutions, manufacturers can secure a competitive edge in this dynamic industry.
CNC press brake machines are set to remain a vital component of modern manufacturing. Now is the time for manufacturers to innovate, invest, and lead the way in shaping the future of sheet metal fabrication.