CNC press brake machines have revolutionized metal bending and fabrication, offering precision, efficiency, and automation. These machines are essential in industries like automotive, aerospace, and heavy machinery, where complex and precise metal bending is required.
However, to maximize their potential, manufacturers need to implement strategies that enhance production efficiency. This guide will explore various methods to optimize the performance of CNC press brake machines, covering aspects such as machine setup, tooling selection, automation, and maintenance.
Understanding CNC Press Brake Machines
CNC press brakes are advanced metal bending machines that use a computerized control system to apply force through a punch and die, shaping metal sheets with high accuracy. Unlike traditional press brakes, CNC models allow for programmable bending sequences, minimizing human error and increasing production efficiency.
These machines come with features such as multi-axis controls, back gauge systems, and real-time monitoring, making them ideal for high-precision manufacturing. By leveraging automation and digital control systems, manufacturers can streamline operations, reduce waste, and improve overall productivity.
However, simply owning a CNC press brake does not guarantee efficiency. It requires proper setup, tooling selection, and adherence to best practices in operation and maintenance.
Key Strategies to Improve Production Efficiency
1. Optimizing Machine Setup and Programming
Proper Machine Calibration
Ensuring that the CNC press brake is correctly calibrated is crucial for consistent results. Operators should verify the alignment of the punch and die to prevent inaccuracies. Misalignment can lead to inconsistent bending angles, material deformation, and an increase in defective products.
The back gauge positioning should also be checked, as it directly affects bending precision. A poorly positioned back gauge can lead to miscalculations in bending angles and faulty components. The hydraulic system pressure must also be monitored to maintain consistent force distribution, preventing issues like over-bending or under-bending, which can compromise product quality.
Efficient Programming Techniques
A well-structured CNC program can reduce cycle times and material wastage. Using advanced CAD/CAM software allows manufacturers to create precise bending programs offline, eliminating unnecessary trial-and-error during setup.
Offline programming reduces machine downtime, allowing operators to focus on actual production rather than manual adjustments. Running a digital simulation before actual production helps detect errors and optimize bending sequences, preventing costly mistakes.
Utilizing batch processing, where multiple parts requiring similar bends are grouped in a single program, minimizes setup changes and enhances efficiency. This strategy significantly reduces downtime, ensuring a smoother and more productive workflow.
2. Selecting the Right Tooling
Matching Tools to Material Type
The choice of punch and die significantly impacts bending precision and material longevity. Using the wrong tooling can result in material cracks, excessive wear, and inaccurate bends. Factors to consider include material thickness, material type, and bend radius requirements.
A die with a wider V-opening is needed for thicker materials to distribute force evenly and prevent cracks. For softer metals like aluminum, different tooling configurations are required compared to high-strength steel to maintain accuracy and minimize tool wear.
Selecting the correct punch radius ensures precise bends and reduces material spring-back, leading to a more efficient production process.
Quick-Change Tooling Systems
Investing in quick-change tooling reduces downtime during tool setup. Features such as automatic clamping mechanisms allow faster tool changes, reducing the time spent manually adjusting the press brake.
Modular tooling systems provide flexibility for different bending operations, allowing manufacturers to switch between production runs quickly without major reconfigurations.
Quick-change tooling not only enhances efficiency but also minimizes operator fatigue by reducing the physical effort required for tooling adjustments. This system is especially beneficial for companies handling multiple small-batch production runs, as it ensures seamless transitions between different bending processes.
3. Enhancing Automation and Process Control
Integration of Robotic Handling
Pairing CNC press brakes with robotic arms can significantly boost productivity. Robotic handling eliminates manual handling errors, ensuring consistent, high-quality production.
Automated systems reduce operator fatigue by taking over repetitive tasks, allowing human workers to focus on quality control and programming. Faster production speeds can be achieved as robots can load and unload materials quickly, minimizing idle time and maximizing output.
In addition, automated material handling reduces the risk of workplace injuries associated with lifting and positioning heavy metal sheets, contributing to a safer working environment.
Smart Sensors and Real-Time Monitoring
Modern CNC press brakes feature advanced technologies such as laser angle measurement systems, ensuring each bend meets specifications without manual measurement. IoT-enabled data collection allows remote monitoring of machine performance, enabling predictive maintenance alerts that prevent unexpected breakdowns.
Real-time monitoring systems track machine efficiency, material usage, and tool wear, allowing operators to make informed decisions that optimize productivity. Implementing real-time tracking and feedback mechanisms can significantly enhance efficiency, ensuring that any potential issues are identified and resolved before they impact production.
4. Implementing Proper Material Handling Techniques
Efficient Material Flow
Improving material handling before and after bending minimizes bottlenecks and accelerates production. Conveyor systems streamline the transportation of metal sheets between workstations, reducing manual labor and potential errors.
Pre-sorting materials based on sheet size and thickness before bending improves workflow efficiency, minimizing the time spent searching for the correct raw materials. Optimizing workstation layout by placing storage racks and tools within easy reach reduces unnecessary movement, allowing operators to focus on production rather than logistics.
Efficient material handling strategies significantly contribute to reducing cycle times and increasing overall output.
5. Preventive Maintenance and Downtime Reduction
Regular Machine Inspection
Routine maintenance prevents unexpected breakdowns that can halt production. Hydraulic system checks ensure fluid levels and pressure remain within optimal ranges, preventing issues such as inconsistent bending force or leaks.
Tooling inspection is crucial; worn-out punches and dies should be replaced to maintain precision and avoid defective parts. Software updates should be performed regularly to keep CNC control systems running smoothly and prevent operational glitches that can disrupt production.
Training Operators for Troubleshooting
Skilled operators can quickly diagnose issues, reducing downtime and improving production efficiency. Training should cover basic CNC error codes and fixes, enabling operators to address minor issues without waiting for technical support. Proper tool handling and storage extend tool life, preventing premature wear and tear.
Emergency response procedures should be well understood so operators can take immediate corrective action in case of unexpected malfunctions. Investing in operator training not only enhances machine efficiency but also ensures a knowledgeable workforce capable of maintaining consistent productivity.
Benefits of Optimized CNC Press Brake Efficiency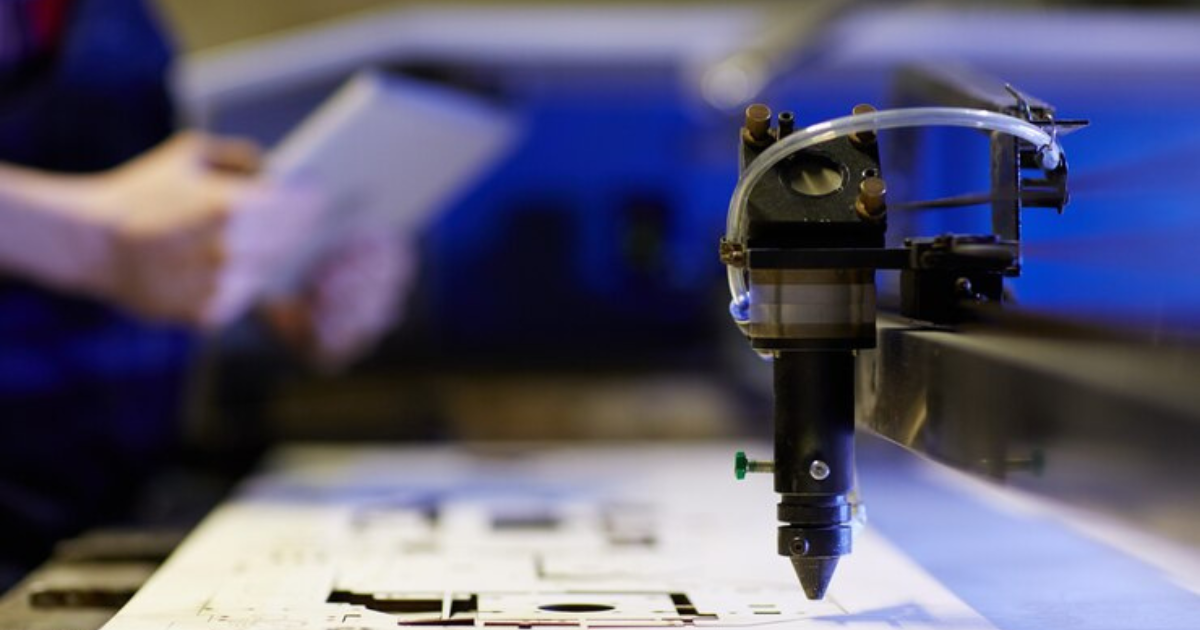
By implementing these strategies, manufacturers can achieve higher production output, faster cycle times, and improved product quality. Precision tooling and calibration reduce defects and rework, lowering material waste and production costs.
Efficient material handling and energy-saving features decrease overhead expenses, leading to greater profitability. Automation minimizes manual lifting and handling risks, enhancing worker safety while improving operational consistency. Optimizing CNC press brake efficiency ensures manufacturers remain competitive in the market while maintaining superior product standards.
Final Thoughts
Improving production efficiency with CNC press brake machines requires a comprehensive approach, encompassing proper setup, tooling optimization, automation, and regular maintenance.
By leveraging advanced programming techniques, selecting the right tools, integrating smart technology, and training operators effectively, manufacturers can maximize the performance of their CNC press brakes. These enhancements lead to reduced cycle times, improved product quality, and significant cost savings, ensuring long-term success in the manufacturing industry.