The longevity and efficiency of sheet metal machinery heavily depend on consistent maintenance. Whether you own an advanced CNC press brake or hydraulic bending equipment, proper care not only extends machine lifespan but also enhances productivity and ensures safety. This guide will dive deep into the essential practices for maintaining different types of sheet metal machinery, including industrial bending equipment, CNC press brakes, and hydraulic shearing machines.
In the competitive industrial sector, whether you are sourcing equipment from a Sheet metal bending machine manufacturer in India or maintaining tools from global suppliers, keeping your machinery in peak condition is crucial for smooth operations. Let’s explore the comprehensive steps you can take to ensure your machinery stays in top shape.
1. Regular Cleaning and Debris Removal: Essential for Longevity
A clean machine is a well-functioning machine. The first and most fundamental step in maintaining your machinery, whether it’s a hydraulic iron worker machine or a press brake, is regular cleaning. Dust, metal shavings, grease, and other debris can accumulate in various parts of the machine, leading to clogging, reduced efficiency, and increased wear and tear. This issue is especially critical for equipment with fine tolerances and high-precision operations, such as CNC-controlled systems.
Machines from a CNC press brake manufacturer require periodic checks and cleanups to ensure that no residual materials hinder the machine’s efficiency. Failing to keep the machine clean can result in defects in sheet metal bending operations, affecting the final product’s accuracy.
Here are some key cleaning tips for different types of sheet metal machinery:
- Hydraulic Machines: Wipe down hydraulic hoses and reservoirs to ensure that there’s no oil spillage or leakage. Regularly remove any grime or dust buildup on hydraulic parts.
- Press Brakes and CNC Equipment: Clean the bending beam, punch, and die to prevent material buildup that could lead to bending inaccuracies.
- Plate Rolling Machines: Make sure to remove any remnants of metal and lubricants from the rolls to avoid surface contamination during operations.
A daily cleaning routine will help avoid potential long-term damage to key components, ultimately reducing machine downtime.
2. Lubrication: The Key to Reducing Wear and Tear
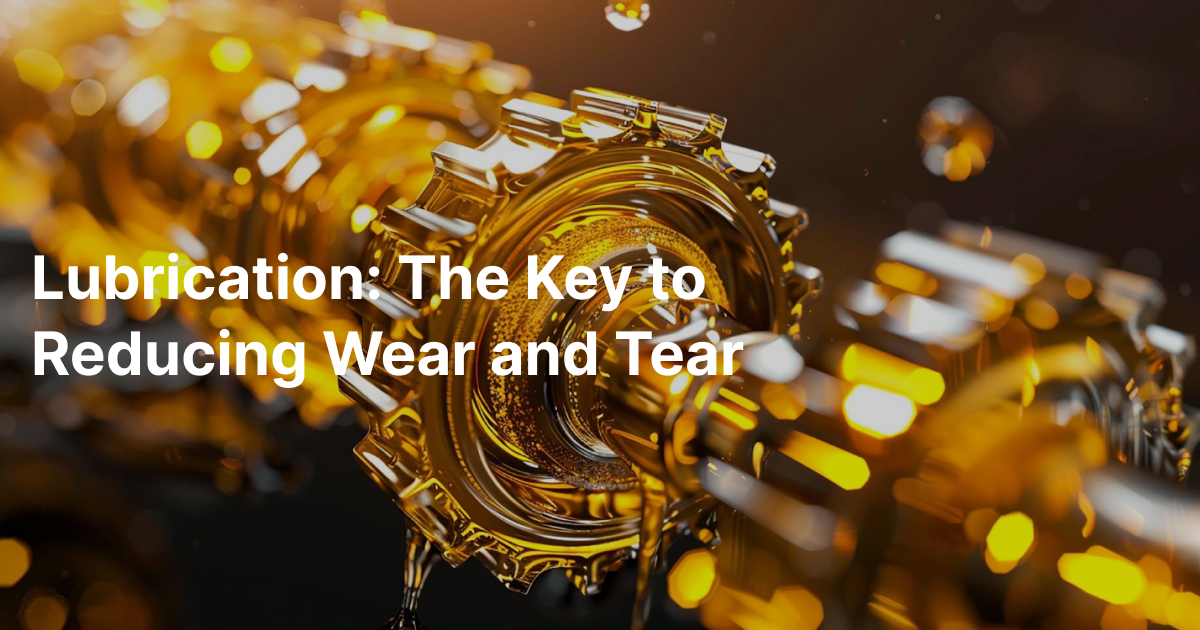
Lubrication plays a critical role in preventing friction between moving parts. Machines like CNC press brakes or hydraulic shearing machines rely on smooth, uninterrupted movement for consistent performance. Without proper lubrication, friction can lead to wear on metal parts, overheating, and, eventually, machine failure. It’s important to use the recommended types of lubricants specified by your CNC press brake manufacturer in Ahmedabad or other providers.
Here’s a breakdown of lubrication practices:
- Hydraulic Bending Machines: Ensure that all pivot points, moving parts, and hydraulic systems are adequately lubricated. Excessive lubrication can lead to oil leakage, while insufficient lubrication can cause overheating and damage to bearings or pistons.
- Press Brakes: Keep the hydraulic press lubricated at the recommended points, including the guide rails, to avoid jamming and frictional wear. For CNC machines, follow the maintenance manual provided by your manufacturer.
- Plate Rolling Machines: Lubricate the roller bearings and moving gears regularly. This ensures that the rollers rotate smoothly and don’t generate unnecessary heat.
Create a lubrication schedule based on the manufacturer’s guidelines, ensuring that you do not over-lubricate, which could attract dirt and debris, or under-lubricate, which could increase friction and cause damage.
3. Calibration and Alignment: Ensuring Precision
Calibration is essential for machines that rely on precision, such as CNC press brakes and other CNC-controlled sheet metal equipment. Machines can lose their accuracy over time due to continuous use. This loss in precision can result in errors in bending, cutting, and shaping, which will ultimately affect product quality.
Regularly scheduled calibration should be performed on machines from any hydraulic CNC bending machine manufacturer to ensure that they maintain their accuracy. Misalignment can lead to issues such as uneven bends or cuts, which can result in material wastage and customer dissatisfaction.
Calibration and alignment steps:
- CNC Press Brake Calibration: Follow your manufacturer’s guidelines for calibrating the press brake’s back gauge, bending axis, and other control settings. Ensure that the die and punch are aligned properly.
- Hydraulic Shearing Machine Calibration: Adjust the blades and gauges for precise cutting operations. Always check for worn-out blades, which can affect the quality of the cut.
- Hydraulic Bending Machines: Test the bending angles frequently to confirm that the machine is producing the correct bend radius.
By keeping your machinery well-calibrated, you minimize waste and ensure that your production runs are consistent, saving both time and resources.
4. Hydraulic System Maintenance: The Heart of Heavy Machinery
Hydraulic systems form the backbone of most heavy-duty sheet metal machinery, including hydraulic shearing machines and hydraulic CNC bending machines. Regularly inspecting and maintaining these systems ensures optimal performance and extends the lifespan of your machinery.
Key areas to focus on in hydraulic system maintenance:
- Hydraulic Fluid: Regularly check the hydraulic fluid levels. Low fluid levels can result in poor system performance, while dirty or contaminated fluid can damage the system. Ensure that you replace the hydraulic fluid as per the manufacturer’s guidelines.
- Hydraulic Hoses and Seals: Inspect hoses for signs of wear, leaks, or cracks. Hydraulic hoses are prone to wear due to pressure and should be replaced promptly if any damage is detected. Leaks can lead to pressure loss, resulting in poor machine performance.
- Filters: Ensure that hydraulic filters are replaced regularly to avoid contamination in the system. Dirty filters can lead to clogs, which affect the overall hydraulic flow.
Maintenance of hydraulic systems requires specialized knowledge, and it is advisable to work closely with the hydraulic press manufacturer or hydraulic CNC bending machine manufacturer to ensure you follow the specific recommendations for your machine.
5. Preventive Maintenance Scheduling: Planning for Downtime
Preventive maintenance involves planning and scheduling routine checks and services for your sheet metal machinery, which helps avoid unexpected breakdowns and costly repairs. It is essential to follow the manufacturer’s maintenance schedules to keep the machine in top working condition. For example, if you have invested in a machine from a CNC press brake manufacturer in India, adhering to their maintenance recommendations will prevent unnecessary machine wear and prolong its lifespan.
Your preventive maintenance plan should include:
- Daily Checks: Perform basic inspections, such as checking for loose bolts, unusual noises, fluid levels, and cleanliness.
- Weekly and Monthly Checks: Inspect the machinery’s core components, such as blades, punches, dies, hydraulic systems, and electrical wiring.
- Annual Maintenance: Schedule professional servicing once a year with the manufacturer or authorized technician. This ensures a thorough review of all systems, including software updates, recalibration, and replacement of any worn-out parts.
A well-organized preventive maintenance schedule reduces the chances of equipment failure, improves productivity, and ensures consistent output quality.
6. Professional Inspections: When to Call the Experts
Despite your best efforts at in-house maintenance, some tasks require the expertise of professionals. Machinery from a hydraulic cutting machine manufacturer or plate rolling machine manufacturer requires specialized attention from technicians trained in that specific equipment.
Periodic professional inspections offer the following advantages:
- Detailed System Analysis: Professional technicians from your hydraulic shearing machine manufacturer can carry out a more detailed inspection of components, identifying any underlying issues that may not be visible to untrained eyes.
- Software Upgrades: For CNC-controlled machines, technicians can install necessary software updates and ensure the control systems are running at their full potential.
- Replacement of Worn Parts: Professionals can assess when parts like belts, hydraulic hoses, or cutting blades need replacing. Using worn-out components can result in damage to the machine or poor-quality products.
Scheduling professional inspections at least once a year ensures that your machines continue to run efficiently, and any potential issues are addressed before they turn into major problems.
7. Operator Training: Invest in Your Workforce
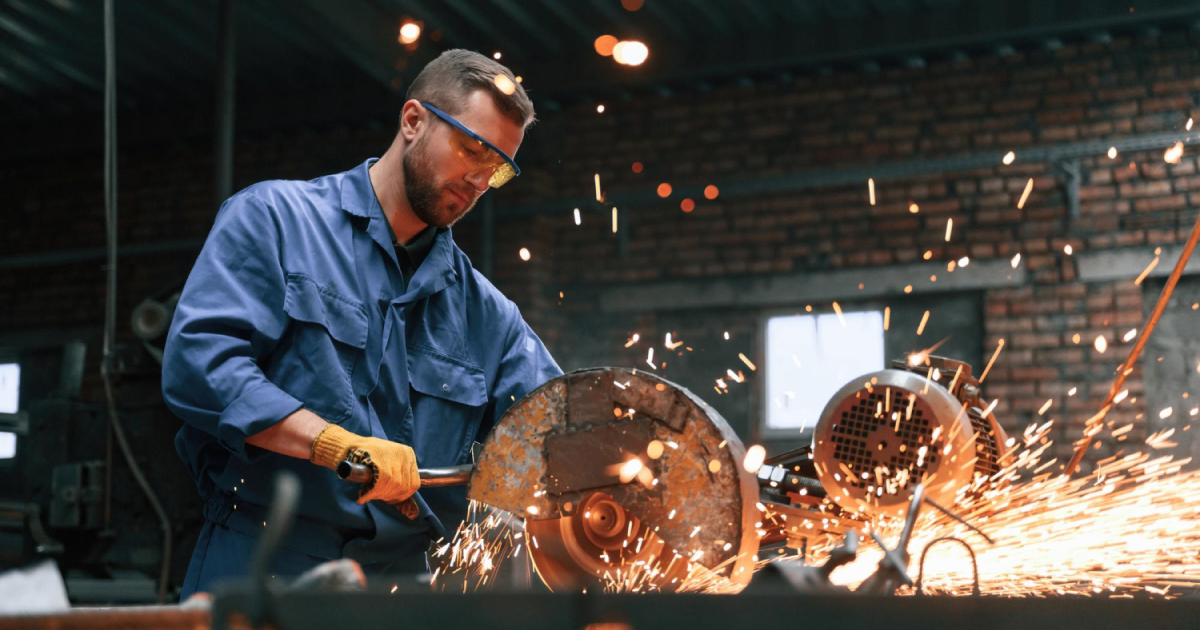
Even with the best-maintained machinery, improper operation can lead to breakdowns and accidents. Ensuring that your workforce is properly trained on operating the machinery can significantly reduce the risk of accidents and machine damage. Operators who understand the equipment’s capabilities and limitations are less likely to misuse it, reducing wear and tear.
Key aspects of operator training include:
- Understanding Machine Controls: Teach operators how to properly use the control systems of CNC machines and hydraulic presses. This includes knowing how to enter the correct programming details for different jobs.
- Safety Practices: Ensure that operators are trained in safety protocols to avoid accidents. They should know how to shut down the machine safely in case of an emergency.
- Basic Maintenance: Operators should also be trained in performing daily checks and minor maintenance tasks, such as cleaning, lubrication, and bolt tightening.
By investing in the training of your machine operators, you minimize operator error, reduce machine downtime, and improve the overall efficiency of your production line.
8. Proper Storage and Environmental Conditions
Another often overlooked aspect of machine maintenance is the environment in which the machinery operates. Machines from a hydraulic iron worker machine manufacturer or CNC press brake manufacturer can degrade quickly if exposed to harsh environmental conditions.
Here are some best practices for storage and operation:
- Temperature Control: Extreme temperatures can affect the hydraulic systems and electronic components of CNC machines. Make sure that your facility has climate control, or at the very least, avoid operating the machine in conditions outside the recommended temperature range.
- Humidity: Excessive moisture in the air can lead to rusting of metal parts and corrosion of electrical components. Keep the machinery in a dry, well-ventilated space to prevent this.
- Storage of Inactive Machinery: If any machine will be out of use for an extended period, ensure it is properly cleaned, lubricated, and covered to protect it from dust and environmental factors.
Maintaining an optimal working environment helps prevent unnecessary wear on your equipment, leading to a longer operational life.
9. Replacing Worn Parts Before Failure
All machines, no matter how well-maintained, will eventually have parts that wear out. The key to minimizing downtime is to replace these parts before they fail entirely. Working with your press brake manufacturer or plate rolling machine manufacturer to source high-quality replacement parts is crucial.
Here are some indicators that parts need replacing:
- Cutting Blades: If your hydraulic cutting machine or shearing machine’s blades begin to show signs of wear, such as jagged edges or reduced cutting efficiency, it’s time for a replacement.
- Hydraulic Hoses: Inspect hoses regularly for signs of leakage or wear. Replacing hoses before they fail will prevent hydraulic fluid loss and system failures.
- Belts and Bearings: Any unusual noises or vibrations in your machine may indicate that belts or bearings need replacing. A well-functioning belt system ensures consistent power transmission within the machine.
Proactively replacing worn parts minimizes machine downtime and reduces the risk of catastrophic equipment failure during production runs.
10. Software and Control System Updates: Stay Current
For modern sheet metal machinery, especially CNC-controlled systems, the software is just as crucial as the mechanical parts. As a CNC press brake manufacturer in India, or CNC press brake manufacturer in Ahmedabad, may offer regular software updates that improve functionality, safety, and performance.
Here’s how you can manage software and control system updates:
- Regular Software Checks: Periodically check for updates from the manufacturer. These updates can include new features, bug fixes, or improved performance algorithms.
- Control System Maintenance: Over time, the control system’s performance can degrade due to outdated software or settings. Reset the system regularly and apply any necessary software patches to keep it running smoothly.
- Backup Data: Make sure to back up machine data and settings before performing any major updates to avoid data loss.
Keeping your software up to date ensures that your machinery benefits from the latest technology advancements, allowing you to maximize productivity.
Conclusion
Maintaining sheet metal machinery is a complex but essential process for any industry relying on high-precision equipment. From regular cleaning and lubrication to professional inspections and part replacements, each step plays a crucial role in ensuring the longevity and reliability of machines from leading manufacturers like a Sheet metal bending machine manufacturer in India. By adhering to the maintenance tips provided, you can significantly reduce downtime, increase the lifespan of your machinery, and improve the quality of your output. Whether you’re working with CNC press brakes, hydraulic shearing machines, or other industrial bending equipment, proper maintenance is the key to sustaining efficient operations and staying competitive in the market.